CONTACT US
Add: No.25, Longpu Road, Dongcheng Development Zone, Huangyan District, Taizhou City, Zhejiang, China
4 Cavity 5L Factory direct sales PET Top Linear Automatic Plastic Bottle Making Machine
Technical Parameters
Project | UNIT | JS-4C-5L |
Production capacity | BPH | 4000-4200 |
Number of Cavity | 4 | |
Clamping force | KN | 720 |
Mould opening stroke | mm | 260 |
Stretch stroke | mm | 350 |
Max. Container Volume | L | 5 |
Max. Neck Size | mm | 39-45 |
Max. Bottle diameter | mm | 180 |
Max. Bottle height | mm | 350 |
Installed Power | Kw | 120 |
Max. Heating Power | Kw | 95 |
Operating Air Pressure | Kg/cm2 | 8 |
Operating Air Consumption | liters/min | 1000 |
Blowing Air Pressure | KG/cm2 | 30-35 |
Blowing Air Consumption | liters/min | 9300 |
Cooling water Pressure | Kg/cm2 | 4-5 |
Cooling water Temperature | °C | 10-20 |
Cooling water Flow | liters/min | 100 |
Measurement (L x W x H) | M | 2.15*2*2.3 |
Machine Weight | Tons | 6 |
Product Introduction:
Discover the versatility and efficiency of our “4 Cavity 5L Factory direct sales PET Plastic Bottle Making Machine,” designed and manufactured by a leading customized plastic bottle making machine manufacturer. This machine is tailored to meet the specific needs of various production environments, showcasing the adaptability of a customized plastic bottle making machine manufacturer. With a production capacity of 4000-4200 bottles per hour, it is equipped to handle mid to high-volume production seamlessly.
Each 4 Cavity 5L machine is a testament to the precision and craftsmanship of a customized plastic bottle making machine manufacturer. The robust clamping force of 720 KN and the precise mould opening stroke of 260 mm ensure consistent and high-quality bottle production. The machine’s installed power of 120 Kw and max heating power of 95 Kw are indicative of its energy-efficient design, which is a hallmark of a reputable customized plastic bottle making machine manufacturer.
Product Advantages
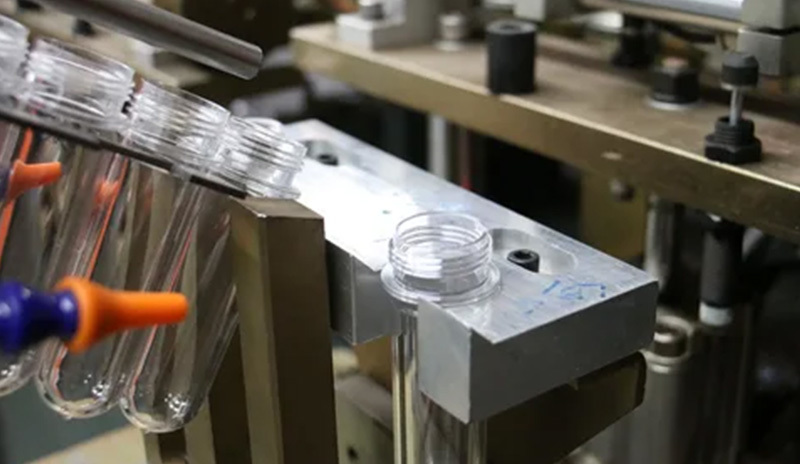
Build over two decades of experience in PET blow molding, Johsean's blow molding solutions are dedicated to delivering excellence in quality, safety, adaptability, competitiveness, and ecological advantages. Our team of experts specializes in tailoring solutions to match your product and production requirements at every stage.

Johsean offering personalized machine designs with options for reduced carbon footprint. Our pioneering, robust, and patented solutions are designed to optimize production efficiency through customized blowing processes to suit your specific demands.
Explore the evolution of our blow molding technology and discover how it can elevate your future PET machine production!
Features
Fully Automated Operation
Energy-saving technology are frequently used into full automatic machines to reduce power usage during operation.
High Production Capacity
Fully automatic blow molding machines are perfect for high-volume production because they can crank out a lot of bottles per minute.
Flexibility
They provide manufacturers versatility because they may be set up to create bottles in a variety of sizes, shapes, and patterns.
Efficient Heating and Cooling Systems
For accurate temperature control during the blow molding process, these machines are outfitted with cutting-edge heating and cooling systems.
User-Friendly Interface
Many models come with user-friendly interfaces that make it simple to change settings, track production, and identify problems.
Energy-Efficient Design
Energy-saving technology are frequently used into full automatic machines to reduce power usage during operation.
Benefits
High Productivity: Full automatic blow molding machines have a remarkable capacity for production, which boosts overall output and shortens production times.
Consistency: Automation guarantees uniform bottle shapes, constant product quality, and fewer manufacturing flaws.
Labor Savings: These machines require little manual assistance, which lowers labor costs and eliminates the need for skilled operators, making them efficient.
Waste reduction: Exact control over the blow molding procedure lowers material waste and raises manufacturing efficiency as a whole.
Customization for Various Industries: Due to their adaptability, these machines are employed in a variety of industries, including the food and beverage, cosmetics, pharmaceutical, and more.
Energy Efficiency: Many models include energy-efficient elements that cut down on power usage and support sustainability programs.
Product Video
Related Products
Product Inquiry
Get in touch with our team promptly and we'll be happy to assistyou help